Extending equipment life: The long-term benefits of proactive fleet maintenance
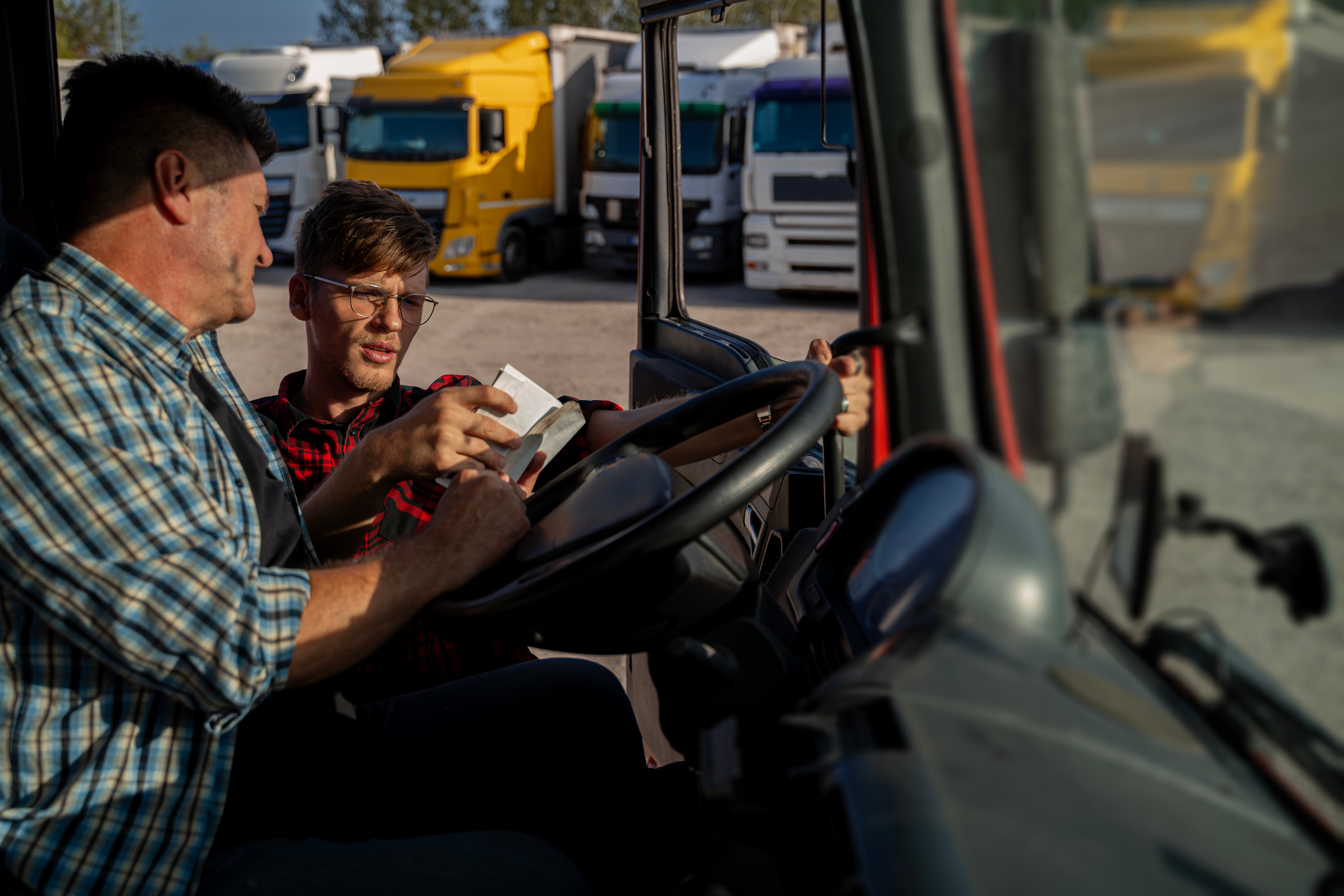
As a seasoned expert in maintenance and warranty compliance at Global Fleet Solutions, I’ve seen firsthand the profound impact that proactive maintenance has on the longevity and reliability of fleet equipment. Maintenance is not merely a routine task—it’s a strategic investment in your fleet’s future. Let me share essential insights on how strategic maintenance can significantly extend the life of your fleet, moving beyond mere cost savings.
The Cost of Cutting Corners:
Often, fleet managers view preventative maintenance as a deferrable expense, hoping to cut immediate costs. Typically, a service might cost around $700, fostering the illusion that skipping a few services could save about $3,000. However, this short-sighted approach leads to more frequent and costly unbudgeted maintenance issues. The truth is stark: perceived savings now can escalate maintenance costs later, with increased downtime and extensive repairs. At GFS, our fleet data acquisition capabilities clearly show that as preventative maintenance (PM) frequency decreases, the frequency of unbudgeted repairs increases.
Understanding Risk Periods:
It’s crucial to recognize the lifecycle risks associated with fleet equipment. The first 4,000 hours of operation generally carry minimal risk, but from 4,000 to 8,000 hours, the likelihood of significant failures spikes. Planning maintenance with these risk periods in mind is key to pre-empting serious issues and effectively extending the operational lifespan of your machinery. Our GFS Strategic Maintenance Management system identifies high-risk, high-failure-probability items and mitigates these risks through diligent maintenance and adherence to warranty requirements. This strategy ensures that when failures occur deep in the machine’s lifecycle, warranty coverage is secured and enforced, rather than merely hoped for from manufacturers. This proactive approach guarantees that our maintenance not only extends the life of your equipment but also upholds the stringent standards set by manufacturers for warranty protection.
Real-world Data on Equipment Failure:
To illustrate, consider our experience with the Hyundai 110D-9 forklift. With a compliant maintenance schedule, the operating cost is about $7.20 per hour. By optimizing the service interval, we’ve reduced this cost to $6.95 per hour. This not only demonstrates cost efficiency but also shows how strategic maintenance timing can significantly enhance equipment longevity.
Setting Up for Success:
Proper setup is foundational to effective maintenance. My role often involves conducting site assessments to ensure that trucks and equipment are optimally configured for their specific applications. This setup is not just about efficiency—it’s also crucial for maintaining warranty compliance and achieving maximum equipment uptime. During these assessments, we identify unique circumstances that the PM plan should accommodate. For instance, working in a concrete production facility should result in more frequent air filter changes to prevent contaminants from clogging the filters and straining the HVAC system or finding an alternate entry into the engine.
The Right Maintenance Strategy:
My maintenance philosophy is straightforward: “Right service, right time, right price.” This approach tailor’s maintenance to the specific needs and usage patterns of each piece of equipment, ensuring that services are both timely and economically sensible. We also incorporate proper battery maintenance into our plans, as batteries are critical to the powertrain systems of a modern electric fleet—an often-overlooked item during service setup that can be very costly later in the machine’s life.
The True Value of Preventative Maintenance:
The overarching benefit of proactive maintenance is its ability to prevent major breakdowns and minimize downtime. By addressing potential issues early, we can avert severe damage that might result from delayed maintenance, thus significantly extending the life of the equipment. This approach also allows us to identify non-rhythmic wear items like steer bushings and lift chains, bring the parts in ahead of planned replacement, and coordinate service times that are the least disruptive to the machine’s core operations.
I hope these insights underscore the importance of proactive maintenance in enhancing the longevity and reliability of your fleet. Our service support systems let you focus on managing your business while we take care of your fleet.