Revamping fleet operations: A success story with Global Fleet Solutions
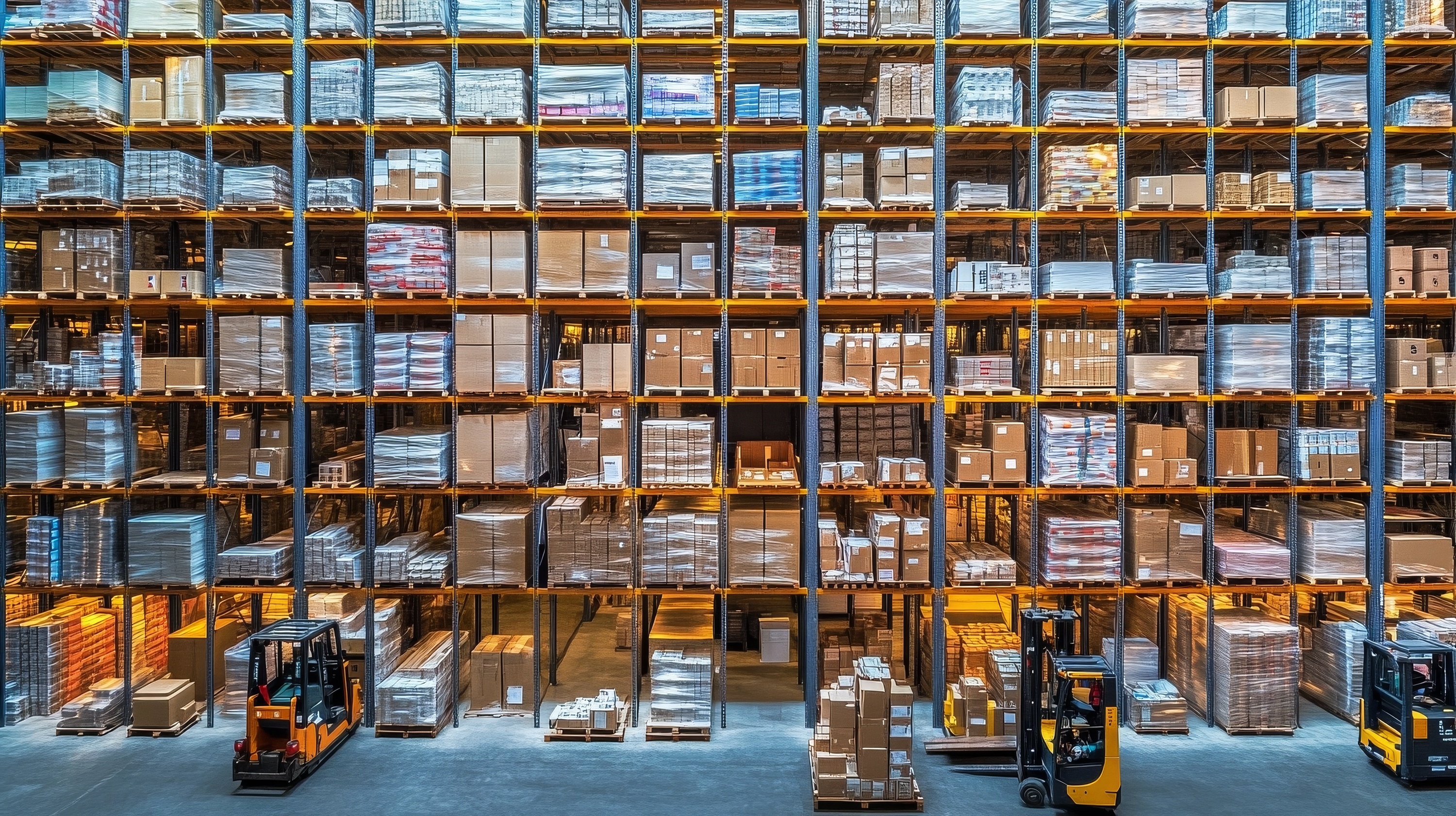
In the competitive lumber industry, efficiency and reliability are crucial. One leading supplier of building materials recently faced operational challenges that threatened their bottom line. This is how they overcame these hurdles with the expertise of Global Fleet Solutions.
The Challenge
The company was struggling with an outdated fleet of materials handling equipment, including forklifts and other critical machinery. Frequent breakdowns and escalating maintenance costs were becoming routine, leading to operational inefficiencies and delays in fulfilling customer orders. These issues not only increased operational costs but also risked damaging the company’s reputation for timely deliveries and reliable service.
Seizing the Opportunity
Realizing the urgent need to modernize their fleet, the company reached out to Global Fleet Solutions. The objective was straightforward: upgrade their materials handling equipment to enhance efficiency, reduce costs, and improve overall operational performance.
A Tailored Solution
Global Fleet Solutions began with a thorough assessment of the company’s existing fleet and operations, identifying key inefficiencies and opportunities for improvement. The team then developed a customized plan that included:
- Fleet Evaluation: A detailed examination of the current equipment to assess performance and identify immediate needs.
- Solution Design: Crafting a tailored plan to introduce new forklifts, telehandlers, and automated guided vehicles (AGVs) to replace outdated machinery.
- Phased Implementation: Managing a careful rollout of new equipment to ensure seamless integration with minimal disruption to ongoing operations.
- Training and Support: Providing extensive training for staff to ensure optimal use of the new equipment and establishing a proactive maintenance schedule to maximize longevity and efficiency.
Remarkable Results
The implementation of Global Fleet Solutions’ customized materials handling solutions resulted in significant improvements for the company:
- Boosted Productivity: The new fleet reduced equipment downtime by 40%, enabling more consistent and efficient warehouse operations.
- Cost Efficiency: Maintenance and repair costs decreased by 30% due to the reliability and efficiency of the new equipment.
- Safety Enhancements: Modern safety features on the new forklifts and AGVs led to a 25% reduction in workplace accidents, creating a safer working environment.
- Improved Customer Satisfaction: Enhanced operational efficiency allowed the company to fulfill orders more quickly, resulting in a 20% increase in customer satisfaction scores.
A Testimonial of Success
“Partnering with Global Fleet Solutions has been a transformative experience for our operations. Their deep understanding of materials handling and their tailored solutions have significantly boosted our productivity and reduced our costs. We’re now better positioned to serve our customers and expand our business,” said the Operations Manager.
This success story highlights the profound impact of modernizing materials handling equipment on operational efficiency and cost management. Through cutting-edge equipment and customized strategies, Global Fleet Solutions helped a leading lumber supplier overcome significant challenges and achieve notable improvements in their operations.
In an industry where every minute counts, the right equipment and strategic partnership can make all the difference. This experience serves as a testament to the power of innovation and expertise in driving business success.